Tailored Injection Molding: Elevating Product Development
In the present challenging business landscape, product development plays a crucial role in the achievement of any company. Organizations are always seeking new ways to develop premium products that meet the needs of their consumers while also streamlining production processes. Among numerous manufacturing techniques, bespoke injection molding is recognized as a strong solution for attaining precision and efficiency. This method not only boosts the quality of the final product but also allows for greater design flexibility, which makes it a preferred choice for numerous industries.
Custom injection molding offers a myriad of benefits that can significantly elevate product development. By utilizing this process, manufacturers can create complex shapes and intricate designs that may be hard or unfeasible to achieve with traditional manufacturing methods. Moreover, the speed and scalability of bespoke injection molding enable a fast turnaround from design to production, permitting businesses to launch their products to market more quickly. As we explore the advantages of bespoke injection molding, it is evident why this method is progressively being adopted by companies looking to remain competitive in the race for innovation.
Grasping Personalized Injection Forming
Personalized injection molding is a production process that allows for the creation of plastic parts and elements customized to specific specifications. This process consists of introducing liquid polymer into a accurately crafted form, in which it cools and hardens into the intended shape. The versatility in designs guarantees that products can have intricate geometries, making it appropriate for a range of applications across different sectors.
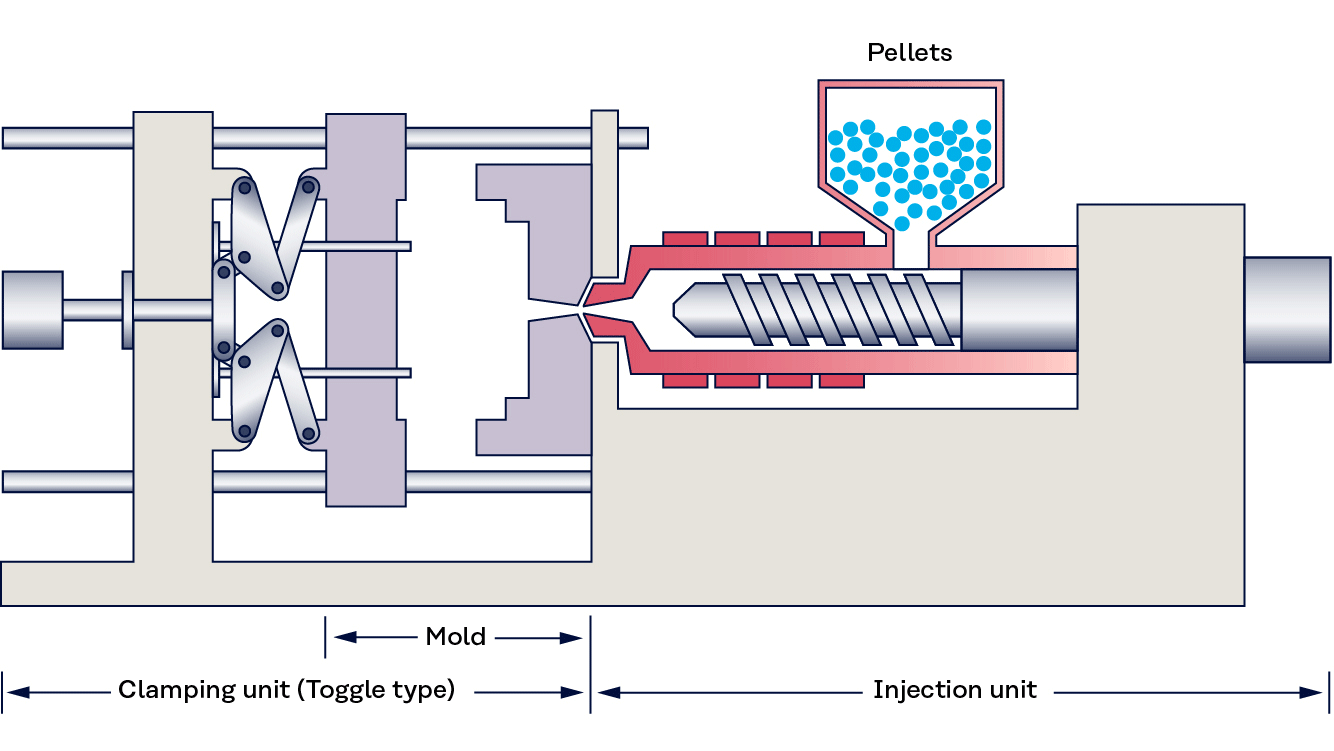
A single significant advantage of custom injection forming lies in its ability to produce large volumes of components with uniform quality. Once the mold has been created, manufacturers can reach swift manufacturing rates, lowering the expense per item as amounts rise. This efficiency makes personalized injectable molding an optimal choice for companies seeking to expand their production without compromising standards or precision.
Moreover, personalized injection forming provides a wide range of substance options, from thermoplastics to thermoset materials, allowing companies to select the best material for their specific use. This flexibility not only enhances the functionality of the finished product but also enables manufacturers to include diverse hues and finishes to meet aesthetic demands. Overall, custom injection molding stands out as a vital process in contemporary product development.
Benefits of Personalized Injection Molding
Personalized injection molding offers significant financial benefits, especially for extensive production runs. The optimization of the process allows for large-scale production at a reduced per-unit cost. Once the first setup of formatures and tools is completed, producing extra units becomes increasingly economical. This scalability makes custom injection molding a popular choice for organizations looking to optimize their fabrication budgets while preserving product quality.
An additional benefit is the styling flexibility that tailored injection molding provides. Manufacturers can create complex shapes and features that may not be viable with alternative production methods. This flexibility enables engineers to innovate and refine their product concepts, ultimately leading to enhanced performance and aesthetics. With the capability to use various materials, including plastics and blends, custom injection molding allows manufacturers to adapt their products to satisfy specific consumer demands.
Moreover, personalized injection molding ensures exceptional product quality and consistency. The precision of the molding process results in uniform products with minimal defects. This consistency is essential for fields that require rigorous quality control, such as the vehicle and pharmaceutical sectors. By employing state-of-the-art technology and skilled expertise, tailored injection molding can produce elements that fulfill exact specifications, fostering faith and satisfaction among customers.
Usage in Product Creation
Custom injection molding acts a crucial role in multiple industries, making it an integral tool for product development. By leveraging this method, organizations can create detailed and precise components tailored to their specific needs. This capability is particularly beneficial in fields such as automotive, consumer electronics, and healthcare, where the demand for high-quality, robust parts is paramount. With the ability to produce complex geometries, custom injection molding allows companies to innovate and enhance their product offerings.
In addition, the speed of custom injection molding significantly speeds up the prototyping phase of product development. Quick production times mean that designs can be evaluated and modified quickly, allowing for prompt feedback and adjustments. This speed not only reduces the time-to-market but also enables organizations to respond promptly to evolving market demands and customer preferences. By employing custom injection molding for initial prototypes, manufacturers can refine their products efficiently before committing to massive production runs.
Ultimately, custom injection molding supports eco-friendly practices in product development. With advancements in materials and processes, manufacturers can minimize scrap and energy consumption during production. The precise nature of the molding process reduces excess material use and confirms that parts are produced exactly as needed. As organizations increasingly prioritize green solutions, embracing custom injection molding can boost their image while contributing to a more sustainable future.